Subaru JDM/Euro EJ207
See [VemsTune camshaft angle control] for primtrig=VR + 4 x VR for camshafts (yes, that is 5 x VR total, with 4 measured and controlled camshafts according to 2 tables - exhaust and intake tables)
This is not right for a EU EJ207
Its crank VR
Left intake camwheel VR
left intake cam 4pulse VR for cam position AVCS
Right intake cam 4pulse VR for cam position AVCS
No exhaustcam control on this engine
Subaru Impreza STI JDM/EURO 2001-2005 (265-280)standard
pink topfeed injectors 550cc
Cop ignition coils firing order 1-3-2-4
the engine is a boxer engine, there for there is right and left
cyl 1+3 is right side
cyl 2+4 is left side
14/5-13
Subaru AVCS dual cam control is working now. We will continuous testing in the near future.
http://www.youtube.com/watch?v=E6KgZdKDGIo
Big thanks to the development team
Testing 2 trigger + 2 cam input
Log file of cam http://www.vems.hu/files/MembersPage/PeterJensen/subaru/v3.3_u004656-2013.05.10-20.06.02_skassa.vemslog
Trigger log http://www.vems.hu/files/MembersPage/PeterJensen/subaru/v3.3_u004656-2013-05-09-17.50.42.triggerlog
The avcs control does not work like its surposed to, the sectric and thirdtric is showing around 167degrees when at idle
- it should be lowered to 20-30 crankdeg with "measure at toothcnt" but it can not be lowered with "measure at toothcount"
- can you show related config(s) and preferrably triggerlog also so it can be reproduced ?
Note: config.strig_validation bits
//See global.h... bit 0,1 camshaft measure count for Subaru and Suzuki VVTI
- define CAMSHAFT_MEASURE_PULSE_CNT_MASK ( _BV(0) + _BV(1) )
- yes tooth 2,5,8 or 11 can be selected
- so the 36-2-2-2 subaru triggercode had traditionally 2 configbits (bottom of config.strig_validation) for setting the "measure tooth at". Back in those days the separate "sectrig measure tooth" and "thirdtrig measure tooth" did not exist (and config was not changed to not cause upgrade problem)
- from fw 1.2.13 (2013-05-13) the "measure tooth at" values are used (and config.strig_validation bit0-1 neglected for subaru and suzuki 36-2-2-2) the same config bytes similarly as for other triggertypes (0-15)
- so when i try to advance it to more then 180degrees it will show a measuretooth of 30-40degrees,this will result in the DutyCycle to go to 100, and the engine will stall.
Is the degrees in the table cam or crank?
- crankdeg (typically can change from 20-80 in a good setup as the cam is advanced, but often 20-56 range is utilized)
Also i cant seem to control the avcs solenoid easy, but maybe it will be fixed when the toothcount measurent is right.
See log for when i try to control it, Thanks Skassa
1: __primary trigger__: Crank trigger Vr (36-2-2-2)
2: __secondary trigger__ : Cam trigger Vr left cam(2pulse)none moving
This is the trigger setup to get the engine running sekventiel
3: __Third trigger__ : Vvti intake cam left side Vr sensor (boxer)4 spots/90degrees moves when avcs is controlled
- any idea at which primtrig tooth does it cross the 0V line (negative-going edge) ?
- no sorry, this is scopeshot while cranking 180rpm
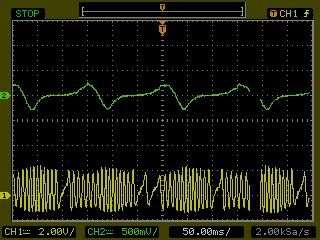
4: __4th trigger__: Vvti intake cam right side Vr sensor (boxer)4 spots/90degrees moves when avcs is controlled. With the "wheelspeed2 calibration=1" config, "secondary trigger position" will reflect the angle of this (so control will use this as feedback signal instead of sectrig)
- any idea at which primtrig tooth does it cross the 0V line (negative-going edge) ?
- no sorry, this is scopeshot while cranking 180rpm
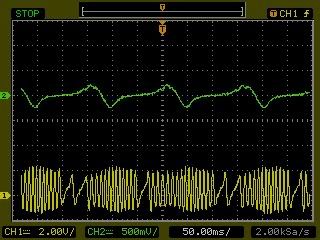
See 1.2.4 on GenBoard/UnderDevelopment/FirmwareChanges , it refers very clearly to where the 3d and 4th trigger 0/5V logiclevel pulses must go in.
This setup uses all 4 vr sensors:
- since "only" 2 VR => HALL LM1815 chips are onboard
- obviously 2 VR => Hall adapters needed (for 3rd and 4th cam sensor inputs).
- Unlike when used for wheelspeed, both __withOUT divider__ (which unfortunately results in MUCH shorter pulsewidth), and because of the shorter pulsewidth filtering capacitor must not be used (must be removed if the controller was ordered with wheelspeed2 input !)
- Trigger4 via VR=>HALL adapter: wheelspeed2 input (without heavy filtering and without divider) used for 4th trigger.
Summary:
- Triggers 3 and 4 seem to be unsuitable for secondary trigger camsync, (because they are indistiguishable in both crankshaft rotations - unlike the sane implementations in BMW, Honda, Suzuki, Ford, ...).
- The cam sensor is good for secondary trigger camsync, but not moving, so useless for camshaft-angle control
- in other words "the good trigger doesn't move with camshaft actuation, the moving ones are not good pattern for syncing".
Firmware mod was implemented in 1.2.4 to use all 4 sensors
see GenBoard/UnderDevelopment/FirmwareChanges : with wheelspeed2 calibration=1 "sectrig position" measures "4th trigger input" (SCL pin similar to 2nd wheelspeed input)
- a good workaround, required because the camsync does not move with cam actuation (and the signals that move are not suitable for camsync as it would make sense like in all other VVTI implementation BMW, Honda, Ford, etc...).
Is this correct?
Yes, seems correct !
- trigger 3 is shown on [VT Help: Motorsport Camshaft-Angle-Control]
- trigger 4 is processor SCL pin (= Atmega128/pin25).
- Warning: although apparently same as wheelspeed2 input ( see InputTrigger/WheelSpeed ), controller must be ordered (or set up) with 4th trigger for Subaru-EJ; because for wheelspeed2 input, agressive filtering is applied that can cause delays (that grow with RPM) when used for trigger, or other problem