VEMS v3.3 installation instructions
These instructions are written for a typical Windows Installation.
The EC36 is the larger Econoseal 36pin plug, and EC18 is the smaller Econoseal plug.
Step One - Connecting Power
The first thing to do is to get a power supply upto the
- EC36-pin25 3A Fused +12v supply
- EC36-pin26 Signal Ground
NOTE: Signal Ground pin has many connections (CAS, TPS, IAT, CLT ...) make provision for this in your wiring loom.
The 3 Power Grounds
- EC36-pin5
- EC36-pin21
- EC36-pin32
- EC36-pin22 this pin is optional, but usually used as an extra GND signal.
Make sure the EC36-pin5 connection does not break during operation. This is the reason for using separate wires: even if 1..2 breaks for some reason (eg. a screw comes loose), at least 2 remains connected.
Before you put any power through the unit use a multimeter to ensure that pins are wired correctly. There is little point in connecting power until the serial connector or LCD screen has been connected.
Step Two - Connecting Serial Port
To allow the connection of the VEMS unit to your PC a serial port plug must be connected as follows.
- EC18-pin14 to DSUB9-pin3
- EC18-pin15 to DSUB9-pin2
- EC36-pin26 to DSUB9-pin5 (GND).
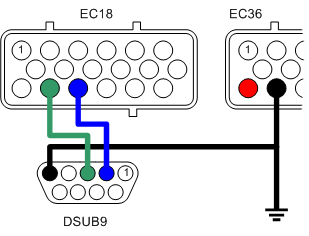
Step ??? - Connecting the LCD
GenBoard/BuildProcedures/LCDconnect
Step Three - Testing the unit
Install required software (Currently mt-r023.zip)
Connect serial lead to unit and PC
Configure MegaTune for the serial port
Connect power to VEMS
Watch system come alive!
Step Four - Connecting the primary trigger (CAS)
Mechanical considerations (need to be written somewhere and referenced from here)
The VR sensing circuitry is very sensative to electrical noise, sheilded cable (coax) must be used and good grounding is vital.
- EC36-pin27 VR+ (central wire in coax)
- EC36-pin26 VR- (sheild and ground)
Sheilding should be grounded to engine block close to the VR Sensor
Step Five 'A' - Connecting the secondary sensor
With the same considerations with the primary trigger regarding electrical noise.
- EC36-pin13 VR+ (central wire in coax)
- EC36-pin26 VR- (sheild and ground)
Step Five - Configuring the system to suit the sensor
[insert config file fragment]
Step Six - Testing the crank sensor
Use MegaTune. Spin the engine. Watch the rpm value.
What to do if it doesn't work.
Step Seven - Connecting the Water Temp. (CLT) Sensor
- EC36-pin14 Signal
- EC36-pin26 Ground (also ground to the engine block close to the sensor)
Step Eight - Connecting the Air Temp. (IAT) Sensor
- EC36-pin2 Signal
- EC36-pin26 Ground (also ground wire to the engine block close to the sensor)
Step Nine - Configuring the temperature sensors
Use EasyTherm to build tables.
Upload tables.
Step Ten - Testing the temperature sensors
Using MegaTune.
Check ambient temperature with thermometer
Check sensors reading on MegaTune or Motuner, compare with thermometer.
Apply known heat (boiling water) and check reading.
Apply known cold (ice) and check reading.
Step Eleven - Connecting the Throttle Position Sensor (TPS)
- EC36-pin28 +5v out
- EC36-pin1 Wiper out (0-5v)
- EC36-pin26 Ground (also ground wire to the engine block close to the sensor)
Step Twelve - Configuring and testing the TPS
MegaTune TPS setup. Steps and screen shots.
Step Thirteen (Optional) - Connecting WBO2 Sensor
- EC18-pin13 to WB6-pin1 (Nerst Cell Signal)
- EC18-pin7 to WB6-pin5 (WBO2 Pump-)
- EC18-pin18 to WB6-pin4 (WBO2 Heater)
- EC18-pin9 to WB6-pin6 (WBO2 Pump+)
Before we plug the wide band in we need to do some tests and calibration, the first is 'Pump Zero DC', you will need to take
a reading with a DVM across pins 5&6 of the Wideband connector. The ideal voltage is zero, to adjust the voltage you will need
to change the values of wbo2_pump_pw_zero in config.txt
Ideally the value should be between 0x64 to 0x66 and the values make a big difference, for example at 0x65 I measured 0.10v
changing to 0x64 resulted in a reading of -0.17 and 0x66 took the reading up to 0.5v
Step Fourteen - Testing WB02 Sensor
Fresh air reading
Configure value to read fresh air O2 level
Step Fifteen (Optional) - Connecting EGT Sensor
Temp. compensated cable, blah blah blah.
Before we can rely on the sensor's readings we need to calibrate VEMS. This is best done using boiling water as we know
that at sea-level this boils at 100degreesC. Make sure that the sensor does not touch the sides of the vessel containing
the boiling water as this will result in an inaccurate reading. At 100degreesC the voltage fromt the sensor (measured
across pins 1&8) should read:4.095mV and AD597's output (pins 4&6) will be 1005mV.
Calibration is required to enable VEMS to display and log the temperature value correctly, there are two values in the
Config file that are used to do this:
egt1_cal=40 # EGT calibration multiplier
egt1_offs=00 # EGT offset (signed e.g. 0xF0 is -1)
(The change values are quite small so try increasing in steps of +/-0x5 initially.)
The EGT reading should be on the LCD screen's first page, to show EGT alone you can use Bray terminal to change to
page 8 by using the command: Manmde08
Put the first few centimeters of the thermocouple onto some ice and watch the value on the scree drop.
Adjust the calibration values until the egt reading is zero. Then using a known temperature heat source (like boiling water) to
Check that the egt value is correct across a wide range.
Example EGT Sensor
Flyback - EC36pin23 very important that EC36pin23 is connected directly (wihtout fuse in between) to all injectors (the injector common + signal).
The injector common + signal is connected with a 10A fuse to a switched +12V supply (often called node15).